IMS / Aluminium
Die stetig steigende Leistungsausbeute bei LEDs und in der Leistungselektronik stellen gleichzeitig auch immer höhere Anforderungen an das Temperaturmanagement der Leiterplatteauch: gedruckte Schaltung, engl.: PCB – Printed circuit boar… Mehr.
Sogenannte IMS Leiterplattenauch: gedruckte Schaltung, engl.: PCB – Printed circuit boar… Mehr (Insulated Metalic Substrate) bieten hier entsprechende Vorteile. Der Metallkern besteht zumeist aus Aluminium, kann aber auch aus Reinkupfer bestehen.
Zum Einen kann die entstehende Wärme direkt in den Kern der Leiterplatteauch: gedruckte Schaltung, engl.: PCB – Printed circuit boar… Mehr abgegeben und bei Bedarf an einen weiteren Kühlkörper abgeführt werden. Zum Anderen bietet eine IMS Leiterplatteauch: gedruckte Schaltung, engl.: PCB – Printed circuit boar… Mehr weitere Vorteile in Bezug auf mechanische Festigkeit.
Die Vorteile liegen unter Anderem in
- Kostenersparnis durch höhere Lebensdauer
- Platzersparnis durch verringerte Kühlmechanismen
- Leistungsdichte durch optimales Wärmemanagement
Im Vergleich zu herkömmlichen Epoxydharzen bietet Aluminium einen um bis zu 30-fach höheren Wert für Wärmeleitfähigkeit. Eine weitere Steigerung des Wärmeleitkoeffizienten kann über den Einsatz von kupferbasiertem Material erreicht werden. Hierdurch ist nochmals eine bis zu 3-fache Erhöhung gegenüber Aluminium erreichbar.
Durch die besseren Wärmeleiteigenschaften gegenüber FR4 lässt sich eine höhere Packungsdichte und entsprechend kleinere Layouts realisieren, was wiederum weitere Vorteile mit sich bringt.
Einsatzgebiete für diese Technologie sind u.a. Hochstrom-anwendungen, Power-LEDs, Kühlungen von Transistoren, SMD- und Power-Leiterplatten. Die hohe Wärmeleitfähigkeit erlaubt eine schnelle und effektive Ableitung anfallender Wärme. In der Automobilindustrie werden seit einiger Zeit verstärkt IMS Leiterplatten eingesetzt.
IMS Leiterplattenauch: gedruckte Schaltung, engl.: PCB – Printed circuit boar… Mehr werden üblicherweise als ein- und doppelseitige Leiterplattenauch: gedruckte Schaltung, engl.: PCB – Printed circuit boar… Mehr mit Durchkontaktierungen gefertigt, sind aber auch als MultilayerMultilayer (Mehrschicht-Technologie):Die Multilayer-Technolo… Mehr verfügbar.
Der grundsätzliche Produktionsprozess entspricht dem von FR4-Leiterplatten.
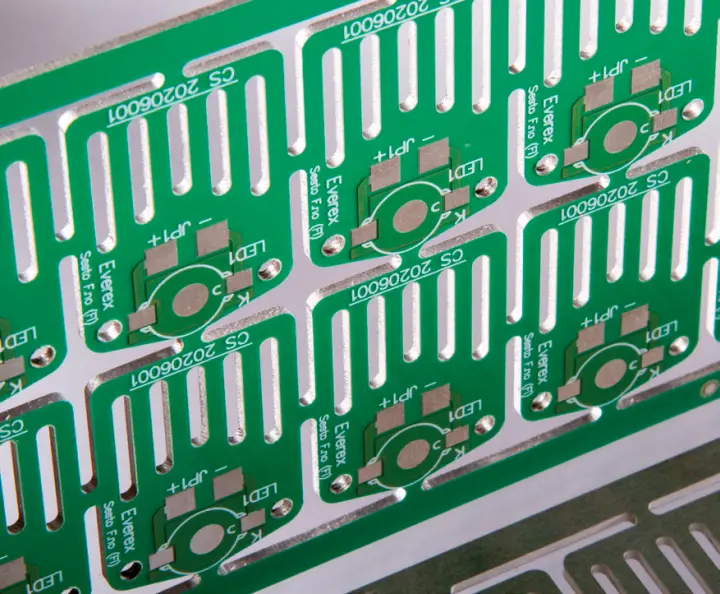
Skizzierter Aufbau einer IMS Leiterplatte
Einseitige Ausführung
Doppelseitige Ausführung
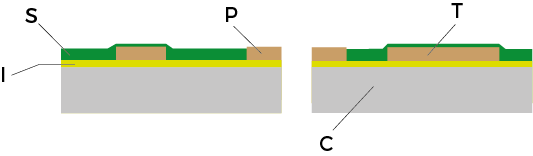
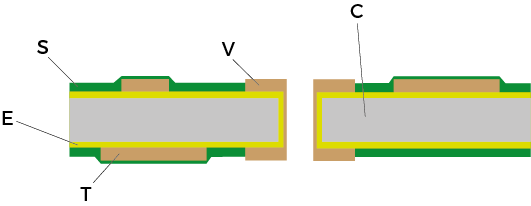
C
T
P
S
I
V
E
Aluminiumkern (Core)
Leiterbahn (Track)
Lötauge (Pad)
Lötstopplack (Soldermask)
Isolation (Insulation)
Durchkontaktierung (Via)
Expoxydharz (Epoxy)
Vorteile einer IMS
- Kostenersparnis durch höhere
Lebensdauer - Platzersparnis durch verringerte
Kühlmechanismen - Leistungsdichte durch optimales
Wärmemanagement
Wärmeleitfähigkeit
Mit sehr einfachen Designs ergeben sich hiermit interessante Möglichkeiten, Wärme effizient zu „managen“ . Die Aluminium-Substrate gibt es üblicherweise in den Stärken zwischen 0,5mm und 3,00 mm.
Die Kupferstärken hängen von weiteren Anforderungen ab und sind von 18μm bis 105μm erhältlich. Die Isolierung zwischen Kupfer und Aluminium beträgt etwa 100 – 150 μm ±10%.
Die kostengünstigste Variante beschränkt sich auf eine einseitige Schaltung, die Wärmeleitfähigkeit von 1,0-2,0W/mK aufweist.
Es gibt unterschiedliche Qualitäten der Wärmeleitfähigkeit, beginnend mit 1,0 W/mK bis zu 4,0 W/mK im Standard und für Spezialanwendungen gar bis 8,0W/mK. Für die gängigen
Anwendungen reichen üblicherweise Materialien mit einem Wert von ca. 1,0-2,0 W/mK.
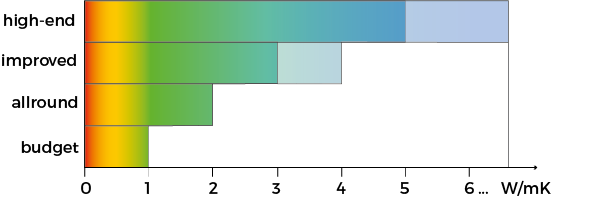
Kombinationsmöglichkeiten
Es bestehen verschiedene Möglichkeiten der Kombination, wie beispielsweise mehrlagige Schaltungen mit einem Aluminiumkern oder einem nachträglich aufgesetzten Aluminium-Substrat, verbunden mit Heatsink-gefüllten Vias in variabler Lagenzahl. Allerdings führt diese Vorgehensweise zu einem Nachteil: Die Wärmeleitfähigkeit sinkt deutlich im Vergleich zu den oben genannten Werten. Dies resultiert einerseits aus der Kombination mit FR4-Material, das eine Wärmeleitfähigkeit von nur etwa 0,3 W/mK aufweist, und andererseits aus den Schwierigkeiten, die Wärme von einem im Inneren liegenden Aluminiumkern abzuleiten.
Die Variante mit dem nach außen aufgesetzten Aluminium bietet den Vorteil, dass die fertige Schaltung mithilfe spezieller wärmeleitender Prepregs auf das Aluminium gepresst werden kann. Diese Prepregs weisen nahezu identische Wärmeleiteigenschaften wie das Aluminium-Substrat auf (ebenfalls 2,0 W/mK), wodurch die Einschränkungen gering sind. Dies eröffnet dem Layouter einen erheblich größeren Spielraum für die Gestaltung.
Vias, die mit Heatsinkpaste gefüllt sind, stellen einen thermisch akzeptablen Wärmeübergang zum Aluminium dar. Diese Technologie ermöglicht die effektivste Ableitung von Wärme, insbesondere bei komplexeren Schaltungen, wo dies unumgänglich ist.
Designregeln
Durch das Aufpressen der Kupferfolie und der nahezu gleich bleibenden chemischen Prozesse zur Erstellung des Leiterbildes ergibt sich bei Leiterbahnbreiten und Abständen keinerlei Einschränkung.
Folgende Kriterien sind für Bohrprozesse zu beachten:
Um einwandfreie Bohrungen ohne Kontakt zum Aluminiumkern gewährleisten zu können ist es notwendig, den Aluminiumträger mit größeren Löchern vorzubohren. Somit ist es möglich, mit Hilfe von Epoxidharz oder Pluggingpaste die spätere Bohrung vom Aluminiumträger getrennt zu halten. Durch dieses Prinzip werden Durchkontaktierungen ebenfalls möglich.
Achtung: größere Bohrzugabe als bei Standard-Leiterplatten!
Eine durchkontaktierte Bohrung durch den Aluminiumträger mit dem Enddurchmesser von 1,0mm wird in der Leiterplattenfertigung allgemein mit einer Zugabe von 0,15mm gebohrt, also 1,15mm. Dadurch wird nach dem Aufbau des Kupfers in der Bohrung der gewünschte Enddurchmesser von 1,00 mm erreicht. Ist die zusätzliche Verpressung mit Aluminium erwünscht, sollte die Bohrung um weitere 0,45mm größer gebohrt werden (1,00+0,15+0,45=1,6mm).
Die Herausforderung ergibt sich, wenn die Lochpositionen in diesem Szenario etwa 1,6 mm voneinander entfernt sind. Auf den ersten Blick scheint ausreichend Platz für Restringe und Abstände vorhanden zu sein. Allerdings kommt es im Aluminiumträger zu Überlappungen, sodass zwischen den Bohrungen kein Aluminium, sondern lediglich Epoxidharz oder Pluggingpaste verbleibt. Dies hat für die Wärmeableitung, die hauptsächlich über die Seiten des Trägers erfolgt, bei wenigen Überschneidungen nur eine geringfügige Auswirkung. Bei einer Vielzahl solcher Überlappungen könnten jedoch ganze Bereiche des Aluminiumträgers hauptsächlich mit weniger wärmeleitenden Harzen gefüllt sein. Im Extremfall könnte dies die Stabilität des Aluminiumträgers beeinträchtigen, und in der Fertigung entsteht das generelle Problem von Bohrerbrüchen aufgrund der überlappenden Bohrungen.
Als Faustformel für die Anordnung von Bohrungen zueinander kann man zur Sicherheit folgendes berücksichtigen
AbstandSpace, Gap Der Leiterbahnabstand, auch als Leiterabstand o… Mehr zweier Bohrmittelpunkte = r1 + r2 + 0,7 [mm]
Generelle Charakteristik
Eigenschaft | Wert/Inhalt |
---|---|
Material | Aluminium | Epoxydharz-Fibreglass |
RoHS | Ja |
UL zertifiziert | Ja, UL 94V-0 |
Standardtoleranz | ±10% |
Leiterplattendicke | 0,5-3,0mm |
Mindestbohrung | 0,8mm |
Dielektrizitätskonstante εR | 3,8 (bei MHz) |
Verlustfaktor | ≤0,03 |
Durchschlagsfestigkeit | >40kV/mm |
Oberflächenwiderstand | 5,0Ω*10e15 |
Kriechstromfestigkeit CTI | >175 |