W tym przewodniku chcielibyśmy przedstawić sugestie i informacje dotyczące wszystkich pytań związanych z projektowaniem idealnego szablonu, optymalnego projektu układu, optymalnego obrazu podkładki i wyboru odpowiedniej grubości szablonu. Nasi eksperci chętnie udzielą porad i pomocy.
Jakość wyciętego laserowo szablonu ma kluczowe znaczenie dla stabilnego procesu produkcji pasty lutowniczej. Objętość, rozmiar i jednorodność osadów lutowniczych są określane przez optymalne dostosowanie projektu padu, wybór odpowiedniej grubości materiału i optymalnych parametrów produkcji.
Należy przestrzegać podstawowych zasad projektowania, takich jak współczynnik powierzchni (obszar zadrukowany w stosunku do powierzchni wewnętrznej ścianki podkładki) i współczynnik kształtu (stosunek szerokości podkładki do grubości szablonu). IPC – Stowarzyszenie Connecting Electronics Industries® opublikowało podstawowe wymagania dotyczące projektowania SMT i powierzchni połączeń SMD w swoich wytycznych IPC-7351B.
Cele
- Doskonałe rezultaty druku
- Precyzyjnie dostosowana ilość partii dla każdego magazynu
- Zapobieganie powstawaniu mostków
szczególnie między małymi osadami lutowniczymi - Unikanie odrywania pasty lutowniczej podczas
Podnoszenie szablonu - Zapobieganie tworzeniu się kulek lutowniczych
- Unikanie efektów kamienia nagrobnego
- Usprawnienie procesu drukowania poprzez
Optymalne rozwijanie pasty lutowniczej
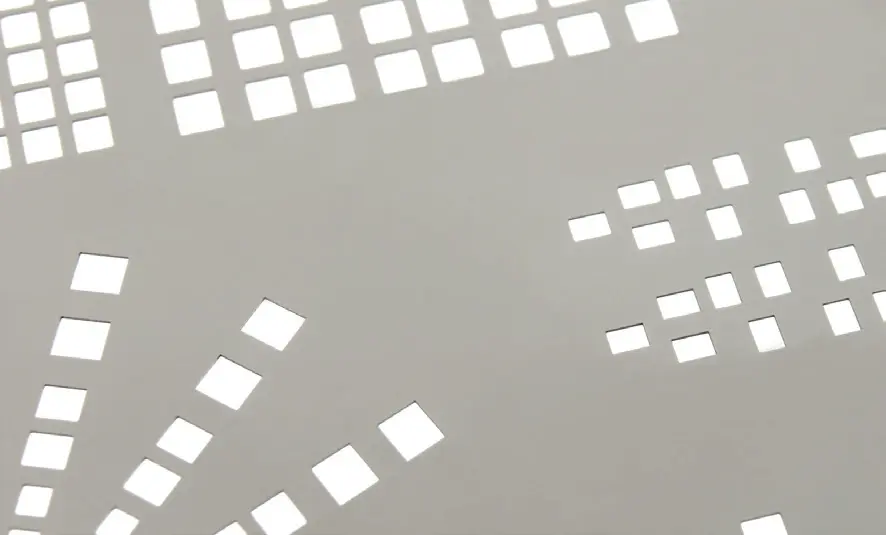
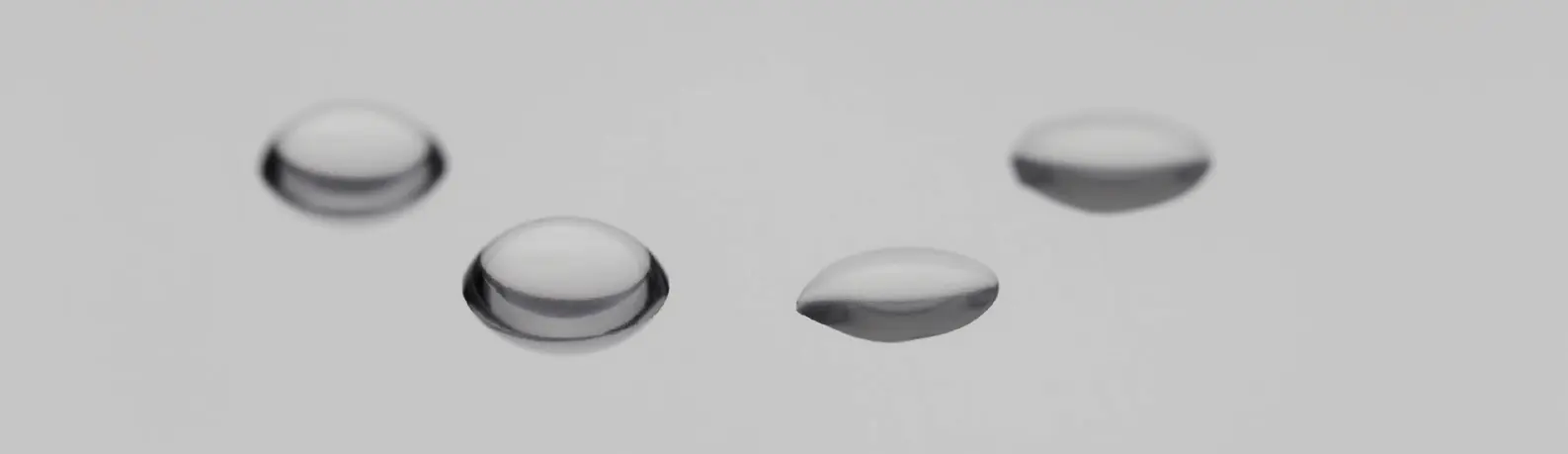
Cięcie laserem
- Precyzyjna blacha o optymalnych właściwościach
- Chropowatość krawędzi 3-4 μm
- Podkładki stożkowo ścięte, skos krawędzi ok. 5°
- Strona wejściowa lasera = bez zadziorów Strona LP nieco szersza ze względu na skos
- Strona wyjścia lasera = strona ssawki
Wynikiem optymalnie zaprojektowanego cięcia laserowego jest znacznie lepsze uwalnianie pasty lutowniczej w porównaniu z pionowymi krawędziami wewnętrznymi padów.
Prawidłowy wybór materiału
- Najmniejszy komponent jest zawsze decydujący
- Praktyczna zasada: szerokość podkładki/1-1,5 = grubość szablonu
- Wspólne w oparciu o średnie komponenty i układ: 120-150μm, 180μm
- Dla BGA, μBGA, FinePitch, Wysoka gęstość: 80μm, 100μm, 120μm, 130μm
Kalkulacja
Współczynnik proporcji
b / d > 1,7
Współczynnik powierzchni
(l x b) / 2x (l + b) x d > 0,8
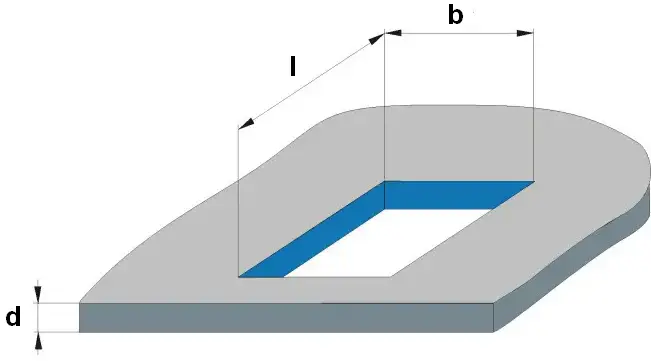
b= szerokość Pad’u, l = długość Pad’u
d = Grubość szablonu
Zalecana grubość szablonu
Kształty komponentów określają dostosowanie geometrii podkładki i grubości szablonu. W poniższej tabeli chcielibyśmy przedstawić wartości orientacyjne, które okazały się dobrymi wartościami empirycznymi opartymi na wielu projektach. Są to wartości przybliżone! Ostateczna decyzja powinna być zawsze podejmowana po zapoznaniu się z kompletnym układem.
Projekt/komponent | Podziałka mm | Szerokość podkładki µm | Zalecane grubość µm |
---|---|---|---|
BGA | 1,25 | 630 | 150-180 |
0,8 | 420 | 150 | |
Finepitch BGA | 1,00 | 500 | 150 |
µBGA | 0,5 | 75-120 | |
IC | 0,5 | 240 | 150 |
0,65 | 320 | 150 | |
0,8 | 380 | 180 | |
>0,8 | 25-30* | 200 | |
01005 | 0,4/0,2 | 20-30* | 120 |
0201 | 0,6/0,3 | 20-30* | 150-180 |
0402 | 1,0/0,5 | 20-30* | 180 |
SCP | 0,65 | 320 | 120 |
PLCC | 1,25 | 150-250 | |
QFP | 0,65 | 150-180 | |
0,5 | 125-150 | ||
0,4 | 100-130 | ||
0,3 | 75-130 |
*Redukcja obwodowa w μm
Przetwarzanie danych
Jakość wyciętego laserowo szablonu ma kluczowe znaczenie dla stabilnego procesu produkcji pasty lutowniczej. Objętość, rozmiar i jednorodność osadów lutowniczych są określane przez optymalne dostosowanie projektu padu, wybór odpowiedniej grubości materiału i optymalnych parametrów produkcji. Należy przestrzegać podstawowych zasad projektowania, takich jak współczynnik powierzchni (obszar zadrukowany w stosunku do powierzchni wewnętrznej ścianki podkładki) i współczynnik kształtu (stosunek szerokości podkładki do grubości szablonu). IPC opublikowało podstawowe wymagania dotyczące konstrukcji SMT i powierzchni połączeń SMD w wytycznych IPC-7351B.
Częste zmiany konstrukcyjne
- Ogólna redukcja wszystkich padów o 10%
- Obwodowe równomierne zmniejszenie padów (np. o 20-50 μm)
- Nadruk: powiększenia w celu osiągnięcia wymaganej ilości w magazynie
- Poszczególne komponenty są traktowane indywidualnie
- Zasada 50:50: szerokość podkładki nie powinna być większa niż szerokość mostu
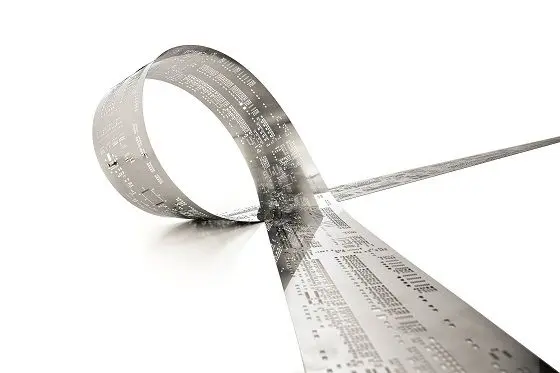