Tested quality is part of a good delivery
Quality is at the heart of every successful electronics production. In a world where technology is constantly changing and the demands on printed circuit boards are constantly increasing, an unwavering commitment to quality is essential. From design to production, quality is at the heart of everything we do.
Printed circuit boards are not just electrical circuits; they are the neural pathways of modern technology. Their quality determines the performance and reliability of electronic devices, from small portable devices to complex industrial applications.
At every step of our manufacturing process, we apply the highest standards to ensure that every PCBauch: gedruckte Schaltung, engl.: PCB – Printed circuit boar… More that leaves our facility meets requirements and exceeds expectations. From the selection of high-quality materials to precise manufacturing and strict quality controls, we focus on excellence.
Our commitment to quality ranges from compliance with international standards to the continuous development of our processes in order to meet changing requirements. We firmly believe that quality is not just a goal, but a continuous journey that we pursue with passion and dedication.
Welcome to PCBworld, where quality is not just a promise, but the basis for your satisfaction and the success of your projects. Discover how we can exceed your PCBauch: gedruckte Schaltung, engl.: PCB – Printed circuit boar… More quality requirements.
Review of the client project in various steps
- DFM Support
- Automatic file import
- Feasibility analysis (Design Rule Check)
- Creating a standard exchange format
- Creation of a management plan optimized for product manufacturing
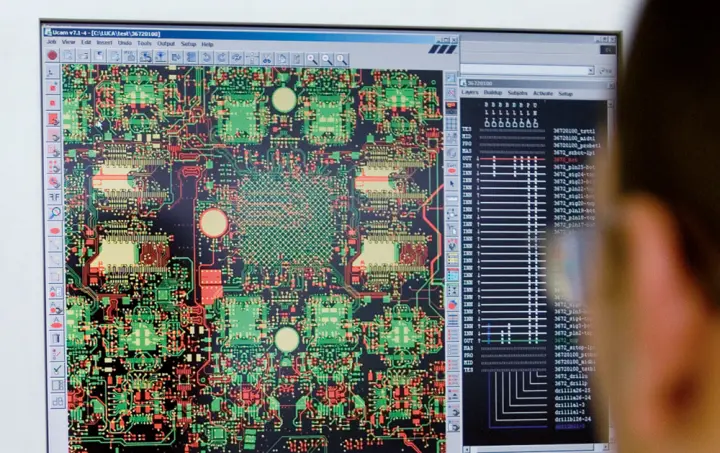
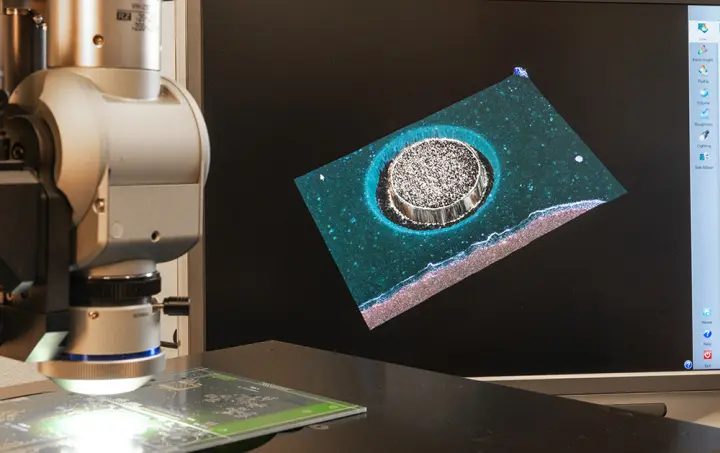
Checking copper thickness
- Copper thickness tests with special instruments
- Composition of surface finishing with XRF instruments
- Refinement of metal thickness tests with XRF instruments
- Micrograph inspection (cross-section)
Mechanical tests
- Dimensional and mechanical testing with optical precision instrument (OGP)
- Micrometric depth controls for scoring lines
- Mechanical machining control (OGP Z-axis)
- Optical 3D controls (Keyence VHX950F)
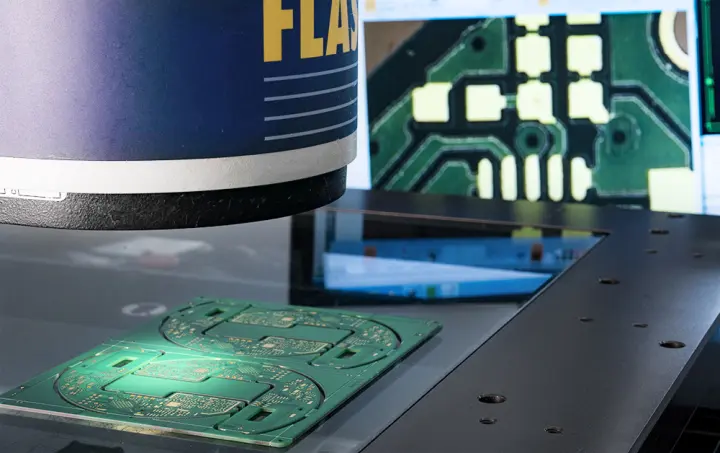
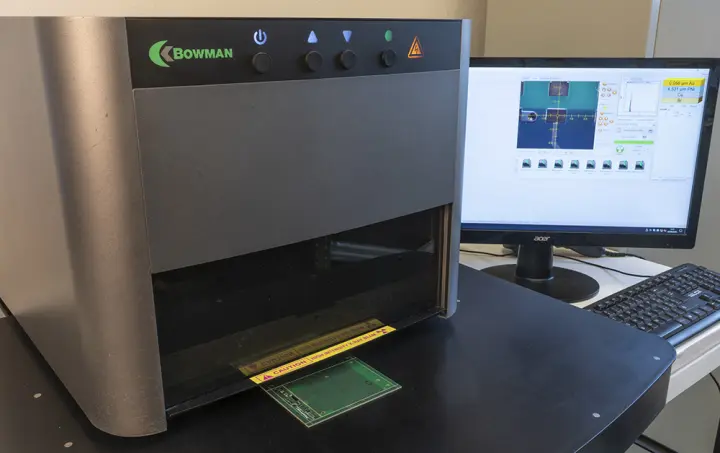
Additional controls
- Impedance control (Z-metric ST300)
- Drill centering tests by X-ray (INSPECTA)
- Ionic contamination tests (TIC)
- Wettability tests for surface finishes (comparative depth test and wetting balance test)
First article inspection report (EMPB / FAR)
At the customer’s request, specific tests can be carried out on the products in order to identify and avoid potential sources of error that could then affect the success of mass production. Corresponding documentation is then created.
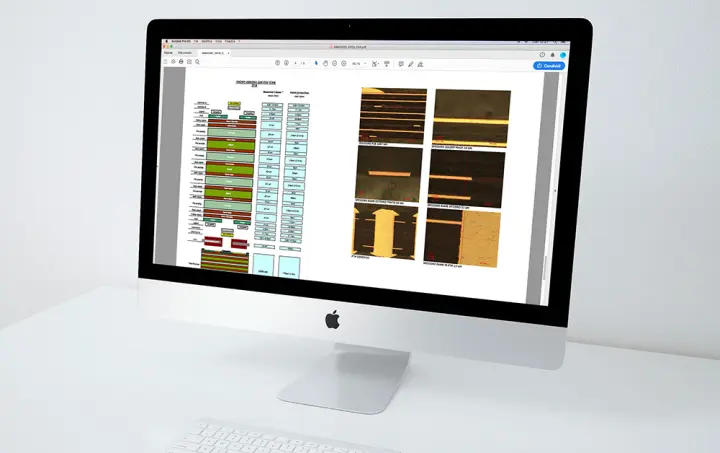
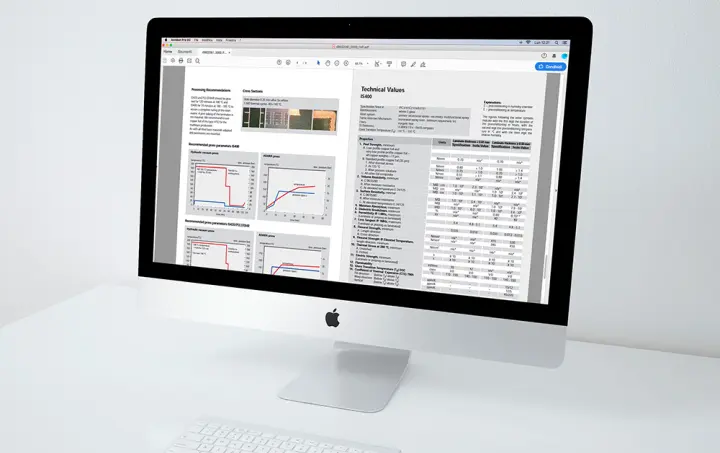
Inspection of the production part
approval procedure (PPAP)
Upon customer request, verification, registration and approval procedures are carried out for the manufacturing process of the sample PCBs, which are individually numbered and documented. In this way, the customer has a series of documents/reports (drawings, materials, processes) on the circuits built in the first sampling phase, which are used as a basis for comparison for subsequent mass productions.